How to Weld Stainless Steel Flange
- OCTOP2
- Aug 15, 2024
- 2 min read
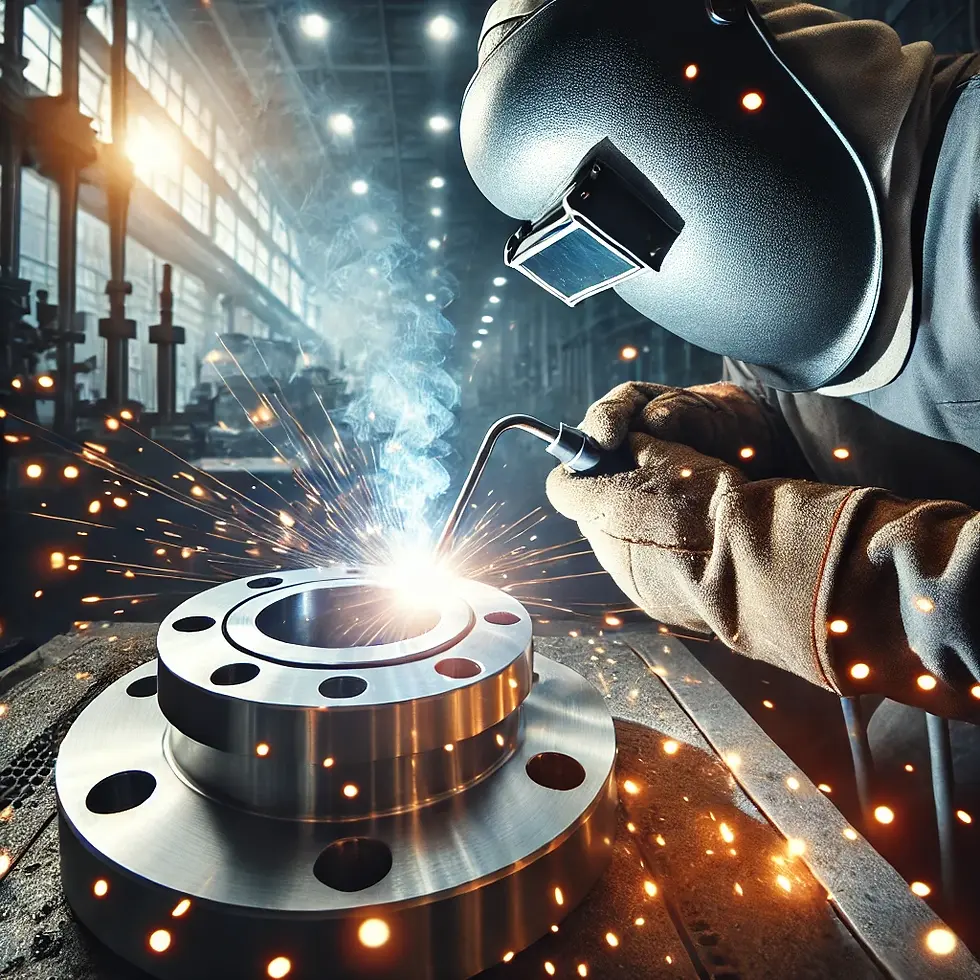
Welding stainless steel flanges requires precision, skill, and the right equipment. Stainless steel is known for its corrosion resistance, but it also requires careful handling during the welding process to maintain its properties. This blog will guide you through the essential steps and considerations when welding a stainless steel flange.
Step 1: Preparation
Material Selection: Ensure that the stainless steel flange and the pipe or fitting you are welding match in terms of material grade. This prevents issues like galvanic corrosion and ensures consistent properties across the weld.
Clean the Flange: Thoroughly clean the flange and the mating surface to remove any dirt, grease, or oxide layers. Stainless steel should be free from contaminants to avoid weld defects like porosity.
Choose the Right Filler Material: Select a filler material that matches the stainless steel grade. For example, for 304 stainless steel, use 308L filler wire. The filler should enhance the corrosion resistance and mechanical properties of the weld.
Set Up Welding Equipment: Depending on the welding method (TIG, MIG, or stick welding), adjust your equipment to the appropriate settings. TIG welding is often preferred for stainless steel due to its precision and control.
Step 2: Welding Process
Tack Welding: Begin with tack welds to hold the flange in place. This ensures alignment and prevents warping during the final welding process. Place the tacks evenly around the flange.
Welding Technique: For stainless steel, use a consistent and controlled welding speed to avoid overheating. Overheating can lead to discoloration and loss of corrosion resistance. Maintain a short arc length and use a back-and-forth motion to ensure even heat distribution.
Shielding Gas: Use a shielding gas like argon or a mix of argon and helium to protect the weld from contamination. Proper gas coverage is essential to prevent oxidation and ensure a clean weld.
Weld in Sections: Depending on the flange size, weld in sections to control heat input. Allow the flange to cool slightly between sections to minimize distortion.
Step 3: Post-Welding
Inspection: Once the welding is complete, inspect the weld visually and through non-destructive testing methods like dye penetrant or ultrasonic testing. Look for any signs of cracks, porosity, or other defects.
Cleaning: Remove any slag or spatter from the weld area. For stainless steel, it is crucial to clean the weld zone to restore its corrosion resistance. Passivation, a chemical treatment, can be used to remove surface contamination and improve corrosion resistance.
Heat Treatment (if necessary): Depending on the application and stainless steel grade, a post-weld heat treatment might be required to relieve stresses and enhance the material's properties.
Final Inspection: Perform a final check to ensure the weld meets the required standards and specifications.
Conclusion
Welding stainless steel flanges is a delicate process that demands attention to detail, proper technique, and the right equipment. By following the steps outlined above, you can achieve a strong, clean, and reliable weld, ensuring the longevity and performance of your stainless steel flange connections.
Comments